Understanding Electric Injection Molding Machines: A Comprehensive Guide
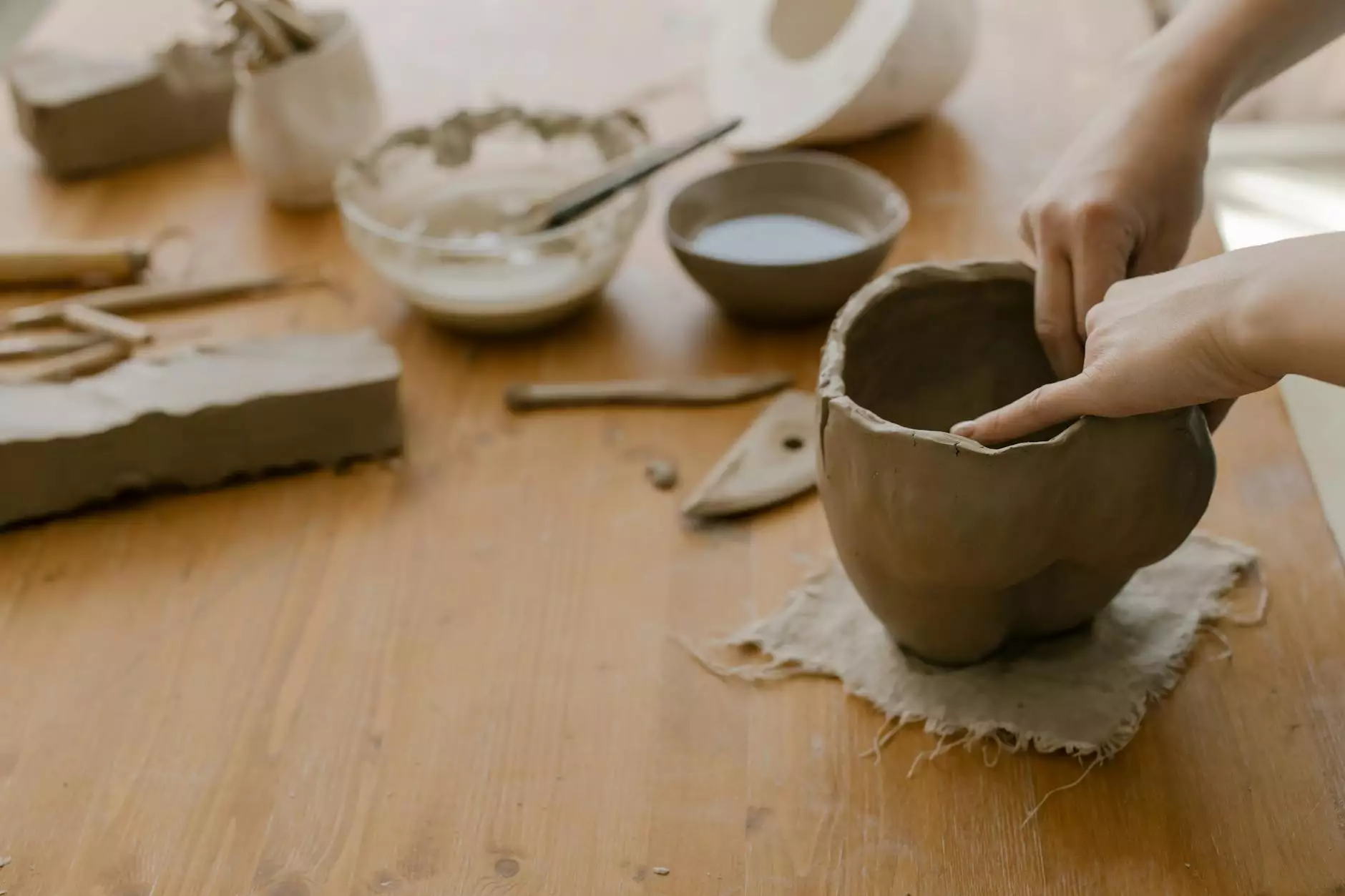
Electric injection molding machines are vital in modern manufacturing, especially within the metal fabrication industry. They offer numerous advantages over traditional hydraulic machines, resulting in improved precision, energy efficiency, and reduced operational costs. In this article, we will delve deep into the workings of electric injection molding machines and highlight why they are becoming the preferred choice in various industrial sectors.
The Basics of Electric Injection Molding Machines
At the core of manufacturing processes, electric injection molding machines are designed to produce plastic parts by injecting molten material into a mold. Unlike their hydraulic counterparts, these machines utilize electric motors for their operation, providing a range of benefits that significantly enhance the efficiency and effectiveness of the molding process.
Key Components of Electric Injection Molding Machines
Understanding the key components of these machines is crucial for appreciating how they work:
- Injection Unit: Responsible for melting and injecting the material into the mold.
- Mold: The design that gives shape to the final product.
- Clamping Unit: Ensures that the mold is tightly closed during injection.
- Control System: Manages the overall operation of the machine for precision and consistency.
The Advantages of Electric Injection Molding Machines
Electric injection molding machines present numerous advantages that make them a favorable choice for manufacturers:
1. Energy Efficiency
These machines consume significantly less energy compared to hydraulic models. By harnessing electric motors, they operate only when necessary, which minimizes power costs. This efficiency not only reduces operational expenses but also aligns with sustainable manufacturing practices.
2. Precision and Consistency
Electric machines provide precise control over the injection process, resulting in consistent quality of parts produced. The ability to control variables like temperature and injection speed with high accuracy leads to fewer defects and better quality assurance.
3. Faster Cycle Times
The speed of electric motors translates to faster injection cycles, enabling manufacturers to increase their productivity. This efficiency is particularly beneficial for businesses that require rapid production times without compromising quality.
4. Low Noise Operation
Electric injection molding machines operate at significantly lower noise levels compared to hydraulic machines. This feature not only creates a more pleasant working environment but also helps in meeting health and safety regulations.
5. Reduced Maintenance Costs
With fewer components subjected to wear and tear, electric injection molding machines typically require less maintenance. The absence of hydraulic oil and related components means there are fewer parts that can malfunction, which reduces downtime and maintenance costs.
Applications of Electric Injection Molding Machines
The versatility of electric injection molding machines allows them to be used across various sectors:
1. Automotive Industry
In the automotive industry, precision and efficiency are paramount. Electric injection molding machines are utilized for producing a variety of components, from interior fittings to critical structural parts, ensuring high quality and durability.
2. Electronics
As the electronics market continues to grow, manufacturers rely on electric injection molding machines for creating intricate parts with tight tolerances. Their ability to work with various polymers makes them ideal for producing durable and reliable electronic housings.
3. Consumer Goods
From household items to personal accessories, electric injection molding provides the versatility needed to produce both simple and complex designs efficiently. Their rapid production capabilities help meet consumer demands in a fast-paced market.
4. Medical Devices
In the medical field, precision is critical. Electric injection molding machines are used for creating components such as syringes, surgical instruments, and other implants where accuracy and consistency are crucial for safety and efficacy.
Why Choose Electric Injection Molding Machines Over Hydraulic Models?
While hydraulic injection molding machines have been the industry standard for years, electric models are carving out a significant niche for themselves. Here’s why you might consider switching:
1. Lower Operational Costs
The combination of energy savings and reduced maintenance costs leads to lower overall operational expenses. For manufacturers looking to optimize their budget, this aspect is crucial.
2. Greater Flexibility
Electric machines can easily adapt to different molds and materials, allowing businesses to diversify their product offerings without significant investment in new machinery.
3. Improved Workplace Safety
The reduced risk of hydraulic oil spills and lower noise levels contribute to a safer working environment. This enhancement in safety standards is increasingly important in today’s manufacturing landscape.
Conclusion: The Future of Manufacturing with Electric Injection Molding Machines
With the ongoing advancements in technology and the increasing emphasis on sustainable manufacturing, electric injection molding machines are positioned to take a more prominent role in the metal fabrication industry. By investing in these machines, manufacturers can enhance their production capabilities, meet the demands of the modern marketplace, and contribute to a more sustainable future.
As businesses continue to strive for efficiency, precision, and reduced operational costs, electric injection molding machines will undoubtedly become a cornerstone in manufacturing facilities across the globe. Explore more about electric injection molding machines at Deep Mould, where innovation meets efficiency.