Understanding the Vital Role of Custom CNC Parts Suppliers
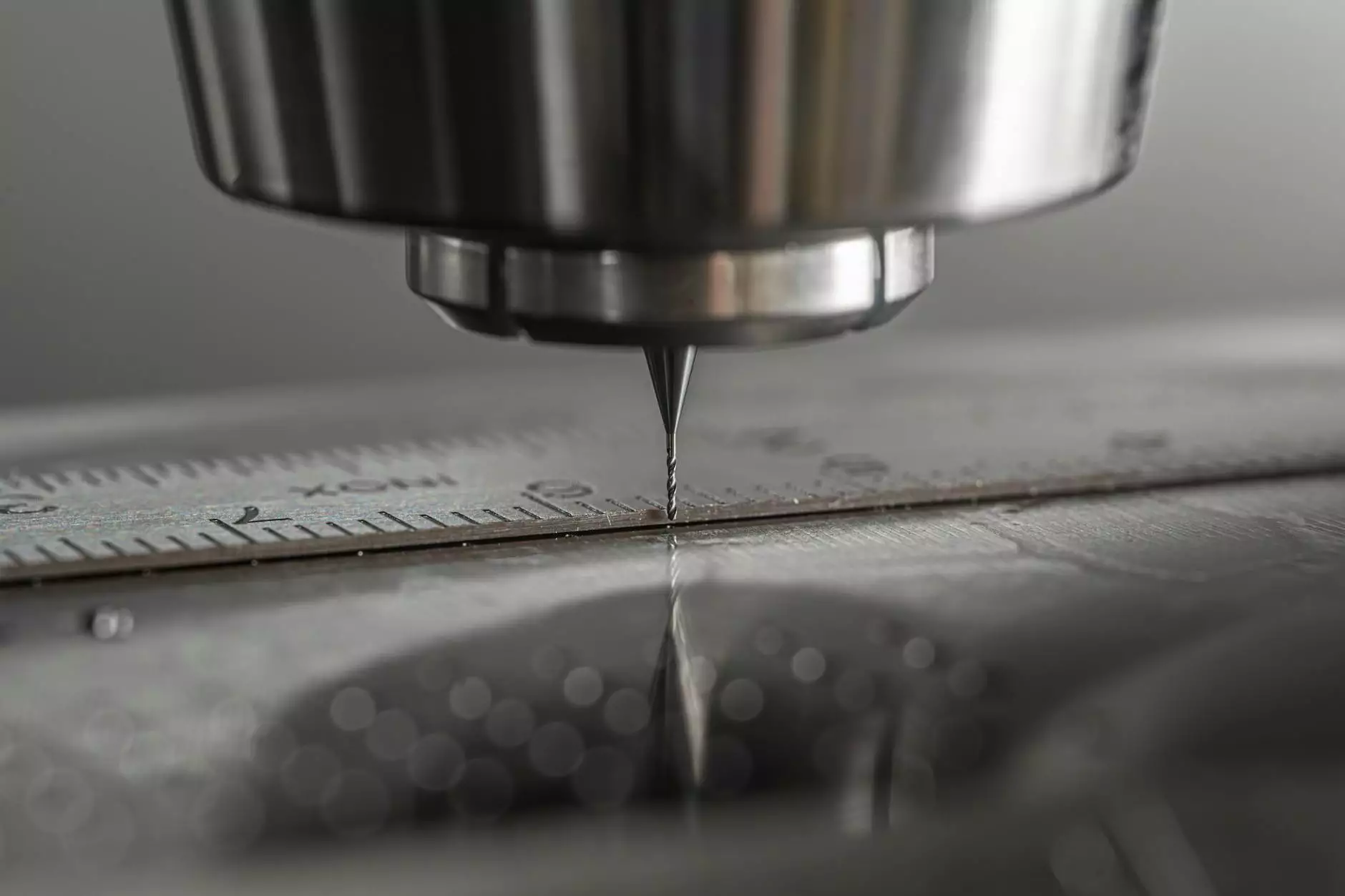
In today’s manufacturing landscape, the demand for precision and quality has never been higher. For businesses looking to create complex components, sourcing from custom CNC parts suppliers has become an essential strategy. Whether you are in the automotive, aerospace, or consumer goods sector, understanding how to effectively source CNC parts can significantly impact your operational success.
The Rise of CNC Machining in Modern Manufacturing
CNC machining stands for Computer Numerical Control machining, a process that automates the manufacturing of parts with remarkable accuracy. This technology has enabled manufacturers to produce intricate parts that are consistent, customizable, and cost-effective. Given its advantages, the industry has experienced a remarkable shift towards utilizing CNC suppliers to streamline production processes.
Key Benefits of Using CNC Machining
- Precision: CNC machines can create parts with tolerances of ±0.01mm, ensuring every component fits perfectly.
- Complex Designs: CNC machining can handle complex geometries that are difficult or impossible to produce with traditional methods.
- Efficiency: Once the design is finalized, CNC machines can produce parts more quickly than manual methods, allowing for shorter lead times.
- Customization: Custom CNC parts suppliers can produce unique parts perfectly tailored to meet client specifications.
- Material Versatility: CNC machining can work with a wide range of materials including metals, plastics, and composites, making it suitable for diverse applications.
Choosing the Right Custom CNC Parts Supplier
Working with the right custom CNC parts suppliers can be a game-changer for your business. Here are some critical factors to consider when selecting a supplier:
1. Expertise and Experience
Look for suppliers with a proven track record in the industry. Companies like DeepMould.net specialize in metal fabrication and have honed their skills over several years. Their experience ensures they understand the intricacies of different materials and manufacturing processes.
2. Quality Assurance
Quality should be a non-negotiable criterion. Suppliers should employ rigorous quality control measures and possess certifications such as ISO 9001, which signifies adherence to quality management standards. Ask about their inspection process and how they handle discrepancies.
3. Technological Capabilities
The technology utilized by the supplier can significantly impact the quality of the parts produced. A state-of-the-art CNC machining setup can reduce production times and enhance precision. Suppliers should continually invest in upgrading their technology to stay competitive.
4. Customer Support
Effective communication is vital throughout the production process. A supplier that is responsive and caters to client needs will foster a more productive partnership. This aspect can greatly influence timelines and the overall success of your projects.
5. Pricing Structure
While cost should not be the only factor considered, it’s essential to understand the pricing structure of your potential suppliers. Compare quotes, but also assess what is included in the price—like tooling, setup fees, and finishing processes.
Exploring the Workflow with Custom CNC Parts Suppliers
Understanding the workflow in working with custom CNC parts suppliers can help businesses streamline their processes. Here’s a detailed look:
Step 1: Design Submission
The process typically begins with the submission of a detailed design. Most suppliers can accommodate a range of formats, including CAD files. It's essential to provide accurate and complete specifications to avoid any miscommunication.
Step 2: Prototyping
Many suppliers offer prototyping services, allowing you to review and test a part before full-scale production. This step is crucial for identifying potential issues and ensuring the final product meets your specifications.
Step 3: Production
Once the prototype is approved, production can begin. Advanced CNC machines can operate continuously to produce parts efficiently, reducing lead times. Suppliers should provide updates on production status, and any potential schedule changes should be communicated promptly.
Step 4: Quality Inspection and Finishing
After production, quality checks are performed to ensure each part meets the agreed standards. This stage may also include finishing processes such as anodizing, plating, or surface treatments that enhance the part's durability and appearance.
Step 5: Delivery and Feedback
Upon completion, the parts are carefully packaged and shipped. Following delivery, suppliers often seek feedback to improve their services and address any concerns, which can lead to a more productive partnership in the future.
The Impact of Custom CNC Parts Suppliers on Your Bottom Line
Partnering with custom CNC parts suppliers can yield substantial benefits for your business. Here’s how:
1. Cost Savings
While upfront costs may seem significant, the efficiency and precision offered by CNC machining can lead to considerable long-term savings. Reduced waste and minimized rework can enhance your overall profitability.
2. Increased Production Speed
With advanced CNC technology, parts can be produced rapidly without sacrificing quality. This acceleration allows businesses to meet market demands and seize more opportunities.
3. Enhanced Product Quality
High-quality parts translate to improved product performance, resulting in increased customer satisfaction and repeat business. Establishing a reliable supply chain for CNC parts ensures that quality remains consistent.
4. Flexibility and Scalability
Custom CNC parts suppliers can accommodate fluctuations in order volume, allowing businesses to scale production up or down as needed. This flexibility ensures that companies can respond effectively to changing market conditions without significant delays.
Future Trends in CNC Machining
The future of CNC machining is bright, with several trends emerging that could reshape the industry:
1. Automation and Robotics
Increasing automation in CNC processes can further enhance efficiency and reduce human error. As robotics technology matures, we can expect to see more machines working in tandem to produce complex products with minimal human intervention.
2. 3D Printing Integration
Integrating CNC machining with 3D printing capabilities can enhance design possibilities and production efficiency. Additive manufacturing can complement traditional machining by producing complex geometries that can be finished with CNC for superior results.
3. Sustainability Practices
Consumers increasingly demand environmentally responsible practices. CNC suppliers are responding by adopting sustainable production methods, such as waste reduction and energy-efficient machining processes, aligning with global sustainability goals.
4. Advanced Materials
The demand for advanced materials, such as composites and high-performance alloys, is growing. Suppliers who can work with these materials will be better positioned to meet the needs of industries seeking innovative solutions.
Conclusion: Partnering with Custom CNC Parts Suppliers
Establishing a partnership with a reputable custom CNC parts supplier like DeepMould.net can empower businesses to enhance their manufacturing processes. By leveraging the precision, speed, and flexibility of CNC machining, you can create a competitive advantage that leads to greater market success.
As the demand for customized solutions continues to rise, understanding how to select and work with CNC suppliers will be crucial for businesses aiming to secure their place in the industry. The journey towards improved efficiency, quality, and innovation starts with the right partnership—take the leap today!